Shunt Ammeters versus Feedback Ammeters
In most instrumentation applications today, two common methods of current measurements are available – the shunt ammeter method and the feedback ammeter method. The shunt ammeter method is commonly used with general-purpose digital multimeters (DMMs) and measures voltage measurements across a shunt resistor. This voltage measurement, combined with the known value of the resistor, yields the current measurement (see Figure 1).
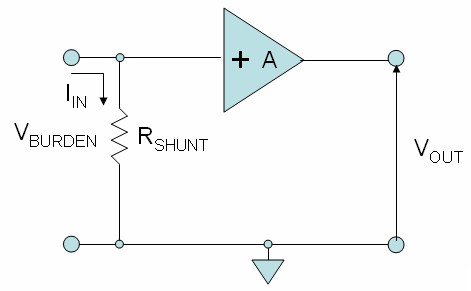
Figure 1. The shunt ammeter method measures the voltage drop across the shunt resistor to calculate the current.
In the shunt ammeter method, low values of Rshunt are chosen to minimize the voltage dropped across the shunt. Although the voltage drop is small, this can have a negative impact on the circuit under test and the measurement.
This voltage drop is known as the voltage burden and is a series voltage error introduced by an ammeter. For current measurements less than approximately 10 mA, it is largely the product of the current you are trying to measure multiplied by the value of the shunt resistance used internally to the ammeter. If the shunt resistor of the ammeter is too large versus the resistances in the circuit under test, the voltage burden causes large errors.
For example, assume you want to measure the input resistance of an A/D converter that has a target specification of 1 MΩ ±2 percent and is limited to test voltages of 0.1 V due to the internal structure of the A/D converter. Using a DMM directly to make this measurement may prove difficult because the test voltage is not generally selectable. Instead, you should apply a known test voltage and measure the resulting current. The measurement might be configured as shown in Figure 2 below.

Figure 2. The above diagram illustrates an example test that measures the leakage current from a 0.1 V source to an A/D converter with 1 MΩ input resistance.
With an input impedance of 1 MΩ and a test voltage of 0.1 V, the leakage current should be exactly 100 nA according to Ohm’s Law (V = IR). However, if you use the shunt ammeter method with a typical burden voltage of 50 mV, the actual measured current is:
Imeasured = (0.1 V – 0.05 V) / 106 = 50 nA
In the above example, the voltage burden causes a 50 percent error in the measured current. Obviously, if the test voltage is smaller, the error percentage increases. At a certain point, the burden voltage becomes too large to make current measurements with any accuracy, and this method breaks down. Even if you could use a test voltage as high as 1 V, the error would still be 5 percent. Because you need better than 2 percent tolerance, this approach will not adapt to your need.
For current measurements more than approximately 10 mA, there are additional terms that compound to increase the value of this voltage burden. For example, for currents in the greater than 100 mA range, the current protection fuse, test leads, and internal DMM wiring add to the resistance presented by the ammeter to the device under test (DUT). These resistances, in combination with the shunt resistance, increase the value of the voltage burden and must be accounted for. The errors can be substantial and cannot be ignored.
Feedback ammeters, on the other hand, use a different method to produce a current measurement (see Figure 3). They use an active transimpedance amplifier to convert the current to a voltage reading. The voltage output is the inverse of the current input multiplied by the value of the feedback resistor, RF.
Vout = -IIN * RF
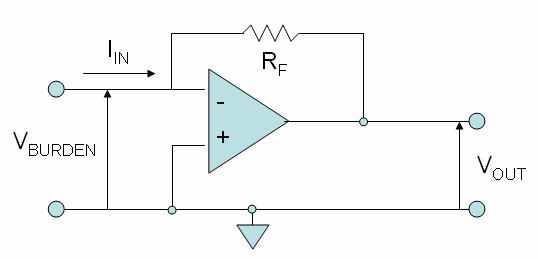
Figure 3. The feedback ammeter method uses an active transimpedance amplifier to convert the current to a voltage with minimal burden voltage on the DUT.
With the feedback ammeter method, voltage burdens are much lower – often in the range of 0.2-2 mV for low-current ranges. For the same A/D leakage measurement and a feedback ammeter with 200 μV of voltage burden, you obtain the following result:
Imeasured = (0.1 V – 0.0002 V)/106 = 99.8 nA
This is only 2 percent error due to voltage burden, as compared to 50 percent error from the shunt ammeter case. The NI PXI-4022 guard and current amplifier module implements a feedback ammeter with less than 20 μV of burden voltage on its 100 nA current range. When combined with the NI PXI-4071 DMM (measuring the output voltage), you can possibly achieve precise current measurement sensitivity at 0.5 pA or better.
Feedback ammeters also have the advantage of measuring low currents much faster. Consider that any instrument, including current measurement devices, display some input capacitance, Cin (see Figure 4). Coupled with this is the cable or probe capacitance, Ccable, because the DUT must somehow connect to the instrument. Recall that in the case of the shunt measurement, a voltage develops across the shunt resistor. The time it takes for the measurement to settle is proportional to the size of Rshunt multiplied by Ctotal. For low currents, you need larger values of Rshunt, perhaps in the Megohm range or greater. The greater the resistance value becomes, the longer the settling time becomes. With a transimpedance amplifier, you need the large resistor, but because it is in the feedback loop of the op amp, the gain “A” of the amplifier scales down the effective resistance presented to the DUT. This gain can be very large – perhaps 1 million or more.
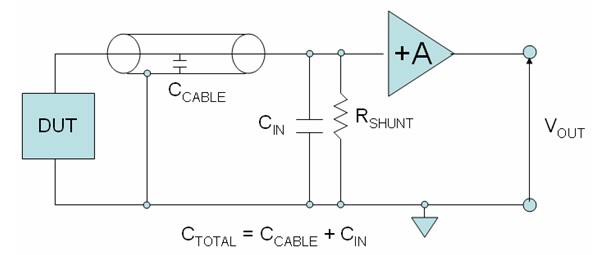
Figure 4. The shunt ammeter method is inherently slower at measuring low currents than the feedback ammeter because of the time required to charge the total capacitance at a high-burden voltage.
By scaling this resistance down by a factor of “A,” the measurement's settling time improves by a factor of “A.” In other words, if the voltage burden is reduced, the input capacitance does not have to be charged much, so the readings settle in much less time.
A practical limitation of the feedback ammeter method is the high-current capability. Feedback ammeters generally are designed to measure currents up to 20 mA or so. At that level, the shunt ammeter method, in which the shunt resistors are small enough to deliver fairly fast settling times, becomes a better option.
If minimizing voltage burden is critical when measuring these high currents, it is sometimes better to use a low-value external shunt resistor embedded into the circuit under test. Sometimes, even measuring the resistance of interconnects within the circuit and then using them as a makeshift shunt effectively embeds the current shunt into the circuit under test. This eliminates errors introduced by routing high currents through long wires and leads back to the measurement system.
Measurement Cabling
With low-current measurements, you must take care with interconnects to ensure maximum noise reduction and optimal shielding. Consider the following when making low-current measurements:
-
50/60 Hz line noise pickup is the most common and considerable source of noise. You can reduce the effect of this noise by using proper cabling, including shielded cables and coaxial cables. DMMs integrated into your system handle the residual line noise rejection very well. At 6½-digit measurement speed, the line noise rejection is typically high enough to virtually eliminate the noise from the signal, giving you confident and accurate readings.
Keep in mind that you cannot make up for poor cable shielding with filtering. The 50/60 Hz line-induced noise can easily saturate the sensitive preamplifier circuitry of any low current ammeter. Once this happens, no amount of filtering can recover measurement accuracy. Therefore, shielded cables are a must.
-
Triboelectric effects arise from the movement of a conductor against an insulator. Cables designed to minimize this effect are available. Reducing cable movement with tie-downs or other fixtures also minimizes this effect.
- Electrostatic pickup is another difficult interference effect. Its roots can once again be traced to poor shielding. Any body is charged with some potential, including the human body. People, hands, and so forth moving near the DUT or cabling during a low-current measurement will induce a current determined by the partial derivative:
I = V dC/dt
in which V is the voltage potential of the body (this could be hundreds or thousands of volts) and dC/dt is the change in capacitance versus time caused by movement near the sensitive measurement setup. This current can be on the order of nA or even uA, which can cause problems with measurement repeatability and stability.
- Piezoelectric effects are caused by the physical deflection of an insulator. Reducing the amount of stress on a device helps to minimize this effect.
- Leakage currents are often the result of contaminants around the device of interest. These contaminants provide an additional current path that causes measurement error. Solder flux and fingerprints (oil, salt, and so on) can be sources of contamination. Many contaminants can be cleaned using alcohol or a similar solvent.
NI offers two cabling accessories that provide the components needed to make low-level measurements. The NI L-1 low-leakage, low-thermal offset cable set consists of two high-impedance prefabricated cables, and the NI L-2 low-leakage, low-thermal offset connectivity set consists of the components needed to make custom high-impedance cables.
Conclusion
This document is meant to serve as an introduction to the basic techniques and methods involved in low-current measurements. You have your choice of measurement methods when approaching current measurements. For current in the μA, nA, or pA range, the feedback ammeter method has distinct advantages. For higher currents, the shunt method is often preferred. Shielding and proper cabling are essential to accurate and repeatable low-current measurements regardless of which method is used.