Connecting an Accelerometer
Before connecting any signals, locate your device pinout.
- Open NI Measurement & Automation Explorer (MAX) and expand Devices and Interfaces.
- Right-click on your device name, and select Device Pinouts.
An IEPE sensor needs an appropriate cable and/or connector to hook into the BNC inputs of the C Series module. Triaxial accelerometers have three outputs, one axis to one acquisition channel, each requiring its own signal conditioning.
The next step is to physically connect the accelerometer to your DSA device. NI DSA devices use BNC or SMB connectors. The center pin of the connector, AI+, provides the DC excitation, when enabled, and the positive input signal connection. The shell of the connector, AI-, provides the excitation return path and the signal ground reference. To minimize ground noise, keep the metal shells of the connectors from touching each other, the DSA device(s), or the chassis/computer.
Configuring an Acceleration Task
You can use MAX to quickly verify the accuracy of your measurement system setup. Using an NI-DAQmx Global Virtual Channel, you can configure an accelerometer measurement without any programming. A virtual channel is a concept of the NI-DAQmx driver architecture used to represent a collection of device property settings that can include a name, a physical channel, input terminal connections, the type of measurement or generation, and scaling information.
Follow these steps to begin:
- With MAX open, select Data Neighborhood and click Create New.
- Select NI-DAQmx Global Virtual Channel and click Next.
- Select Acquire Signals»Analog Input»Acceleration.
- Select ai0 or whichever physical channel you have connected to your accelerometer. For multiple channels, hold down the Shift key and select all the channels being used. A physical channel is a terminal or pin at which you can measure or generate an analog or digital signal.
- Click Next and enter a name for the global virtual channel or leave the default.
- Click Finish and you should see the following screen in MAX:
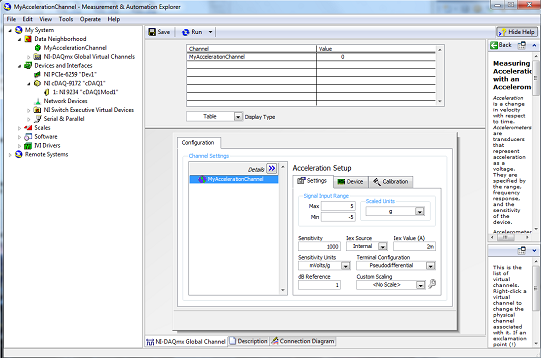
- On the Settings tab, type in the minimum and maximum acceleration values you expect to read from your accelerometer (-5 g to 5 g by default).
- Type in the sensitivity value of the sensor. This value is in the units you specify with the sensitivity units input. Refer to sensor documentation to determine this value.
- Select the source of excitation (Iex Source):
- External—Any excitation source other than the built-in excitation source of the device.
- Internal—Use the built-in excitation source of the device.
- None—Supply no excitation to the virtual channel.
- Specify the excitation value (Iex Value (A)).
- Select your terminal configuration. Terminal configuration specifies the grounding mode used for the virtual channel. You can choose Differential or Pseudodifferential depending on your device (see above).
- Type in the dB Reference value. This is the reference value used when results are computed in decibels. dB Reference is expressed in the selected engineering units.
- Click the Device tab and choose your Coupling Mode (AC or DC).
Testing the Signal
-
With MAX still open, click back on the NI-DAQmx Global Virtual Channel tab and click on the Run button. You see the acceleration value of your measurement displayed at the top of the screen.
You can choose to view the signal in tabular form or as a graph by selecting
Graph from the
Display Type pull-down menu. You also have the option of saving your NI-DAQmx Global Virtual Channel should you wish to refer to this configuration screen again in the future.
LabVIEW Example for Measuring Vibration
Once you have configured the system properly, you can acquire and visualize data using the LabVIEW graphical programming environment.
You can locate examples for your device by clicking Help in LabVIEW Toolbar»Find Examples. Once in NI Example Finder, there is a pull-down menu in the bottom left-hand corner where you can pick your specific module. When you have chosen your module, check the Limit Results to Hardware box. Now all relevant examples for your module are shown.
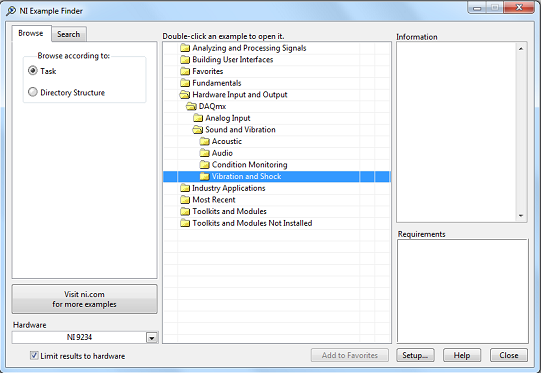
With the Level Meter (DAQmx).vi shown below, you can continually acquire data from the specified channel. The data is scaled to engineering units. The energy content of the signal is then measured using three different methods:
A. Compute the power spectrum and then find the power in band
B. Compute the RMS level of the signal
C. Compute the running RMS level of the signal
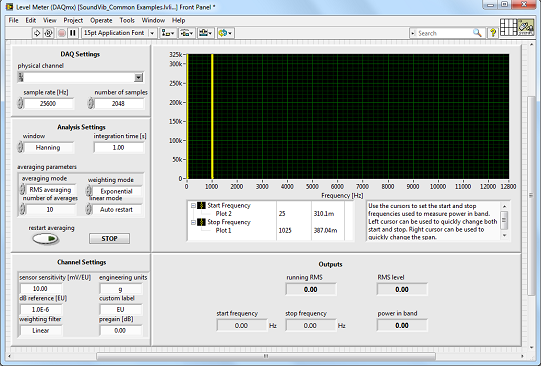