Solution
First lets understand the creep corrosion: Sulfur can attack copper (and to a lesser extent silver) in a way that leads to molecular migration. Sulfur dioxide and water from the air condense onto a PCB surface and form weak sulfuric acid H2SO4. Oxidized copper reacts with the acid to form copper sulfide Cu2S. This compound precipitates into dendrites that grow across the PCB surface, leading to electrical shorts.

Around 45-55% relative humidity is ideal for this attack, and any amount of sulfur is sufficient. Many customers maintain their manufacturing facilities around 50% RH to minimize static electricity, and sulfur can be found in the environment of customers that use or process materials such as rubber or ceramic, or those that have electroplating equipment. It can also be found in otherwise benign facilities near those that process such materials.
This corrosion attacks exposed silver and copper, such as non-plugged vias, ESD strips, press-fit connectors, guard traces, and test points. Pads with solder on them are generally safe. Areas with increased air flow will see greater attack as more sulfur and moisture are brought to the board.
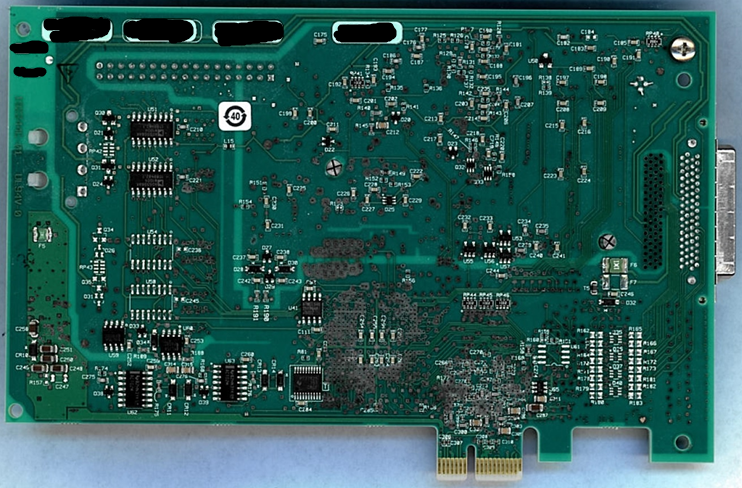
Creep corrosion filaments start as a high-resistance short, so boards will often continue operating despite excessive corrosion. Over time the increased density of the dendrites reduces the resistance until failure, at which time a customer might find that not only that board but all their boards show damage.
How can customers eliminate or mitigate creep corrosion?The primary means to eliminate creep corrosion is to eliminate the sulfur in the environment. Customers with processes that release sulfur into their facility should capture and process/vent that sulfur rather than let it build in the environment. If necessary, electrical equipment such as NI products can be enclosed and supplied with clean external air with constant positive pressure.